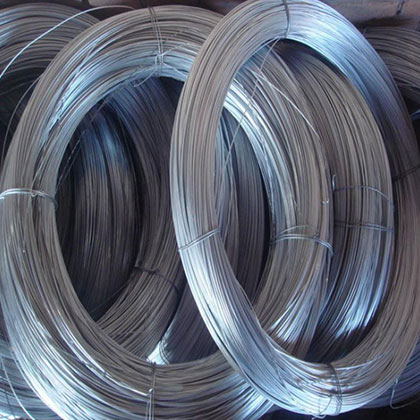
Powder coating entails the electrostatic application of a dry powder to the surface of the metal workpiece,followed by curing of the product to form a protective layer. Benefits of powder coating include the ability to form thicker coatings than is possible with paint or other liquid coatings. The dry application prevents sagging or running. Powder coating is also an environmentally friendly process, as the coatings contain no solvents and do not release volatile organic compounds (VOC) into the atmosphere.
Hot-dip galvanizing involves the immersion of iron or steel workpieces into a bath of molten zinc heated to a temperature of approximately 840 F. The zinc alloys with the surface of the base metal to form a protective coating. The zinc reacts with the oxygen in the atmosphere to form zinc oxide. The most important benefit of hot-dip galvanization is enhanced protection against corrosion.
A primary difference between galvanized and powder coating is the way they protect the surface of the workpiece. Galvanization provides sacrificial protection, meaning the coating will absorb corrosive materials before they can reach the metal object. Powder coating works by forming a protective barrier that prevents destructive materials from penetrating and reaching the surface.
The ability of hot-dip galvanization to deter corrosion makes it an excellent choice for protecting outdoor objects that are vulnerable to the elements, such as iron and steel gates, fences and guardrails. However, powder coating offers greater flexibility for decorative applications — coatings are available in numerous colors and textures — making it better suited for indoor products. Various pretreatment methods are also available to bolster the powder coating’s corrosion protection capabilities.